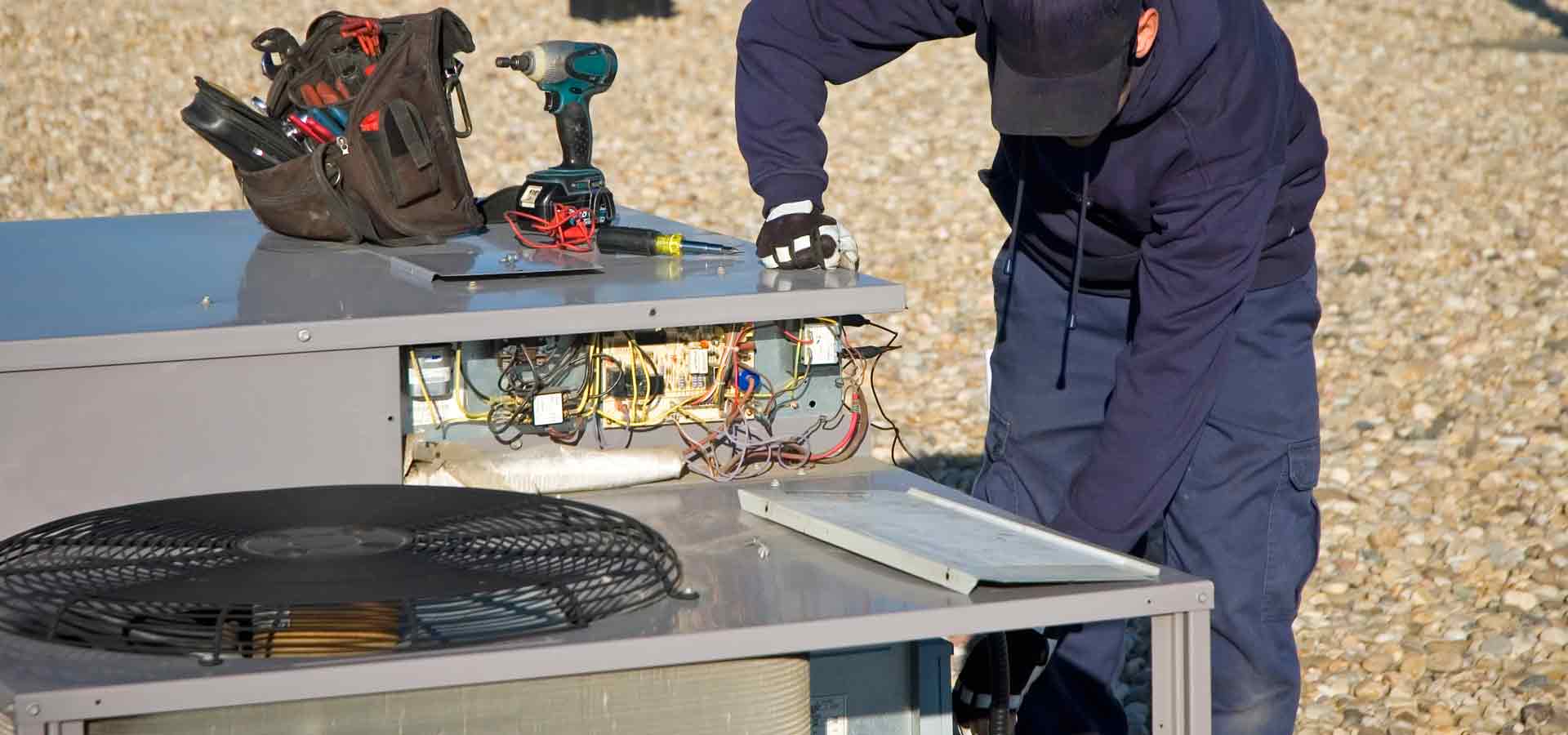
Maintain Mechanical - What is Preventative Maintenance of Your Mechanical Systems, and Why is it Important?
Our mission is not to misinform to maximize revenue with costly repairs or delay fixing or failing to highlight issues in order to appear to lower costs in the short term but rather develop long-lasting mutually beneficial relationships. Our goal in creating a partnership with owners and boards is to advise on the best path to maintain and service building equipment in order to protect assets and investments. Our mandate is to provide our services with honesty, integrity, and communication as the building blocks of trust.
What is preventative maintenance?
Contrary to popular belief, preventative maintenance does not equate to stopping equipment failures and unexpected repairs. It would be dishonest of us to say that no repairs on equipment will be necessary in the future. Preventative maintenance is required to ensure that a building’s equipment reaches its intended lifespan. Our role is to highlight small deficiencies or design oversights before they become larger and more costly problems. Preventative maintenance on building equipment can be compared to the maintenance of a vehicle; it’s far cheaper and safer to inspect and replace a car’s brake pads when required rather than leaving it until other parts of the braking system are affected.
Why is preventative maintenance important?
Preventative maintenance is an all-encompassing term that includes some added values that may not be immediately obvious to the client. Some of these include:
- Increased comfort – When a piece of equipment is operating as per design, the building’s occupants will be more comfortable and relaxed in their environment.
- Increased energy efficiency – Ensuring pieces of equipment are clean from debris and are set at the proper set points helps lower utility costs overall. There has been a shift in the industry to move away from mid-efficiency pieces of equipment to high-efficiency pieces to lower utility costs even further. We can help prepare a cost-benefit analysis to determine which course of action is the best for any building. It’s difficult to forecast the exact savings, as each building has a unique combination of equipment that can make forecasting difficult, however, we have seen a minimum of a 5% utility saving, and as much as a 25% utility saving from year to year, after an efficiency upgrade.
Not only can we ensure that a building has optimal set points for its heating and cooling systems, we can modify them based on the occupants’ feedback and the building’s ‘personality’ to ensure that we maintain resident comfort, while lowering utility costs as much as possible. Fine tuning these set points will be an ongoing adjustment process, but as we gain more experience with a building we can optimise your systems and settings to find that happy medium between resident comfort and utility costs. - Lifespan of equipment – The main purpose of a preventative maintenance program is to ensure that any building’s equipment reaches its full lifespan, as laid out in the reserve fund study. Often, it’s possible to extend these lifespans to help build up reserve funds, but a cost-benefit analysis should be performed once these pieces of equipment reach their intended lifespans.
A lifespan for a large piece of building equipment is typically 25 years, but the construction, mechanics, and controls for these types of equipment can change drastically over that time period as the technology improves. This can result in considerable efficiencies gained by simply replacing these components. As is often the case, continuing to repair them becomes an added expense for owners and boards. Our experience and expertise can provide insight into the most cost-effective way to stage necessary large-scale replacements. - Improved air quality – Replacing filters in common heating, ventilation, and air conditioning (H.V.A.C) equipment can drastically improve efficiency and comfort. Our technicians are trained to highlight any abnormal filter conditions, which allows us to be proactive in increasing the efficiency of the system. Often, in the industry, filters are replaced every quarter, regardless of their condition. Filter condition depends on various parameters. As filter quality has increased over the years, we have seen filters become fouled sooner than we saw previously. Our gold package automatically includes monthly filter replacements. Although this will increase filter costs, early replacement will lower utility costs from the units not having to work as hard to overcome the pressure loss from a fouled filter.
Decreased emergency repairs – Catching small issues before they become larger issues helps lower emergency on-demand repairs. Often, emergency work is charged at a premium for the labour rates, and sourcing parts during an emergency can be troublesome. Completing preventative maintenance will help reduce emergency issues from occurring or resulting in larger catastrophic failures.
Contact Maintain Mechanical today to get a custom quote and to find out more about our packages. Below, is also a list of our most common packaged preventative maintenance options. By clicking on one of these options you will see more information including what is offered in each package.